The Surprising Pros & Cons Of Drum Sander
Drum sanders, also called wide belt sanders, are a powerful woodworking tool used to sand and flatten large panels and boards. The sanding drum provides an efficient way to smooth and level wood surfaces. But drum sanders also come with some downsides to factor in.
This comprehensive guide will dive into the key pros and cons of drum sanders to help you decide if investing in one is worthwhile. We’ll look at the benefits they provide for flattening and smoothing wood as well as considerations around safety, dust control, costs, and more.
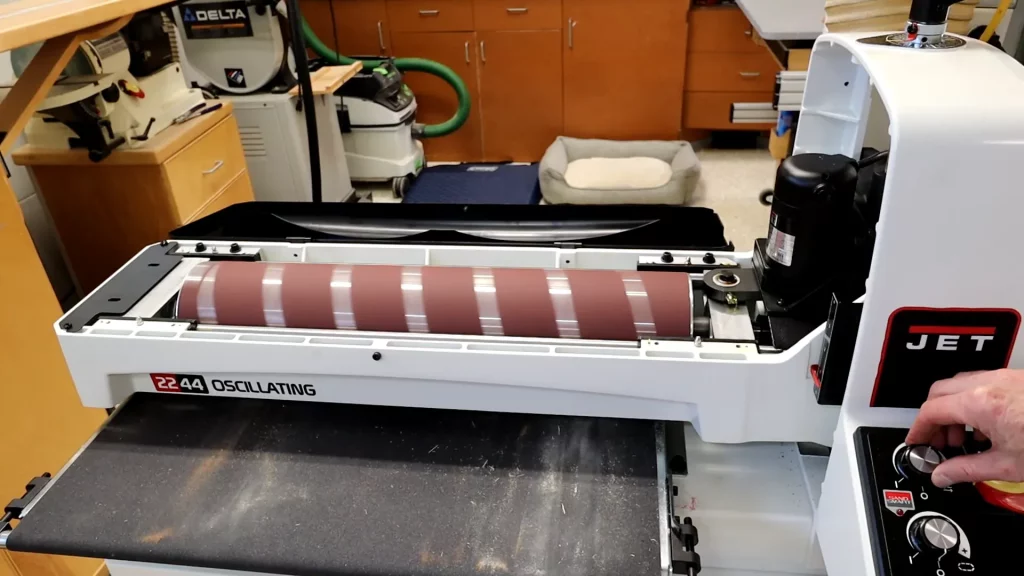
Main Advantages of Drum Sanders
Quick Processing of Wide Boards
One of the biggest pros of drum sanders is their ability to quickly process large, wide boards. The typical 4-6” sanding belt lets you sand the full width of boards like tabletops or doors in just one or two passes. This makes them incredibly efficient compared to other sanders when working with oversized pieces.
Drum sanders are built to remove material rapidly from large workpieces without rounding edges or creating dips as smaller tools can. You don’t have to carefully work a narrow sander across the full width of a board. Just feed it through the drum sander and you’ve smoothly sanded the entire surface area quickly.
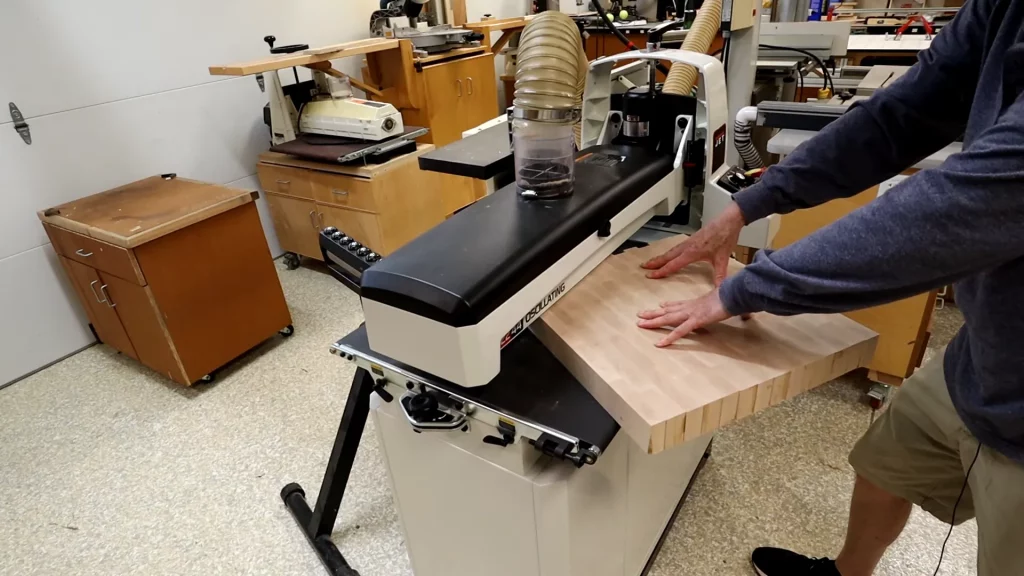
Even, Consistent Sanding Finish
Another major benefit is the consistent, even finish drum sanders provide. The spinning drum beneath the wide sanding belt results in a uniform sanding pattern across the board. This prevents swirl marks, valleys, and other inconsistencies you can get from hand or orbital sanding.
As the board passes under the drum, any high or low spots get levelled out. Drum sanders leave surfaces flat and smooth across their full width. For sanding panels wider than your planer, they excel at providing a consistent finish.
Models for Different Shop Needs
Drum sanders come in a range of sizes and models to suit different uses. On the small side, benchtop units with 22-24” drums work for smaller hobbyist projects. Larger standalone floor models feature 30-50” drums capable of high-volume production work.
Specialty edge drum sanders help with vertical profiles. Different speeds, dust collection options, and digital thickness gauges provide flexibility. With this range, you can likely find a drum sander well-matched to your typical workload and workpiece sizes.
Extremely Smooth Finishes
The combination of the spinning drum and sandpaper creates an exceptionally smooth finish. While the exact amount of sanding scratches depends on grit, drum sanders can produce finish-ready surfaces themselves in many cases.
Using finer grits like 150 or 220, a light final pass can eliminate any need for additional hand sanding on solid wood. For veneered panels, drum sanders gently abrade the veneer without tear out. The smooth sanded surface they leave reduces later finishing steps.
Relatively Simple Operation
While powerful tools requiring safety awareness, drum sanders have a relatively simple operation compared to other woodworking machines. The basic process involves adjusting the conveyor bed height, turning on the sander, and feeding your workpiece through.
The shallow learning curve makes it easier for both novice and experienced woodworkers to make use of drum sanders effectively. You do need proper workpiece support on infeed and outfeed, but the actual sanding process itself is straightforward.
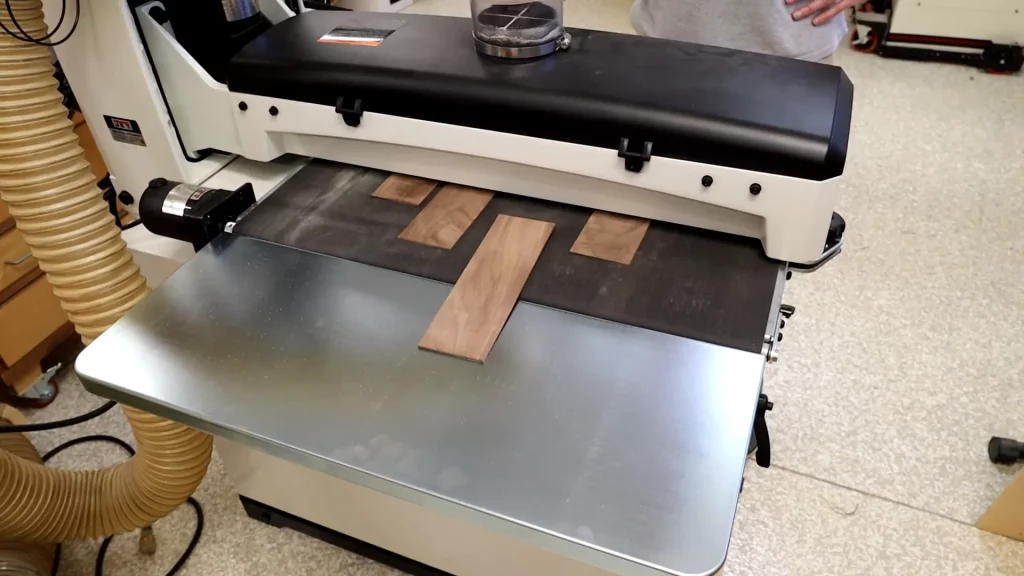
Downsides to Consider
While they provide useful capabilities for flattening and smoothing boards, drum sanders also come with some downsides to factor in when deciding if purchasing one makes sense for your woodworking.
Safety Concerns
One disadvantage is drum sanders contain large spinning abrasive components that pose a safety risk. Feeding boards without full attention risks fingers or hands getting sanded by the belt. Loose clothes, jewelry, long hair also pose entanglement hazards.
Staying focused, keeping hands clear of the sanding belt, and using a slow feed rate is imperative for safe operation. Drum sanders require extreme care and caution to operate safely without injuries. New woodworkers should take time to thoroughly learn proper practices.
Lots of Fine Dust Created
The high sanding volume of drum sanders creates loads of fine dust. This dust coats your workshop and is also unhealthy to breathe in without protective equipment. Even robust dust collectors struggle to contain all the airborne dust from aggressive drum sanding.
Proper dust containment is crucial not only for shop cleanliness but also for respiratory health. Be prepared to enhance dust collection and/or wear a protective dust mask to work cleanly with a drum sander. Removing the quantities of dust they produce takes effort.
Substantial Space Requirements
Drum sanders take up significant space that should be factored in. Benchtop models require over 30” depth. Standalone floor models are larger still at 100-200+ lbs. You need room for adequate infeed and outfeed support also.
Having enough space for the sander itself plus proper workpiece support is key. For smaller home shops, this can be a challenge. Drum sanders perform best with plenty of stable surrounding space to handle infeed/outfeed of full sheets and long boards.
Difficult for Thin or Warped Stock
While great for smoothing wide boards, drum sanders struggle with thin stock and warped lumber. The strong downward pressure can cause major deflection in thin material. This leads to an uneven finish or potential tearing.
Similarly, warped boards with sections not in flat contact with the conveyor belt easily get grabbed aggressively. For thin or irregular wood, hand planes followed by finish sanding often perform better. Drum sanders excel on thicker flat boards but have limitations.
Primarily for Flat Faces Only
The straight orientation of the sanding drum also means drum sanders are not well-suited for sanding shaped edges and profiles. While edge drum sanders exist, the most common models mainly focus on flat panel faces.
Specialty sanders like spindle sanders or oscillating edge belt sanders adapt better to shaping edges and arched profiles. Drum sanders are great for broad surfaces but have limits sanding edges of tabletops, rounded components, and decorative shapes.
Infeed and Outfeed Support Needed
Feeding long or oversized panels through a drum sander requires solid infeed and outfeed support. You need tables the full width of the sander before and after to support the workpiece’s trailing end.
Letting the workpiece droop at the end causes friction burn against the belt. Adequate support along the board’s full length makes for smooth sanding without kickback from an unsupported end catching. Having space for support tables is key.
Frequent Belt Changes Needed
The fast wear of sandpaper in drum sanders means you must replace belts somewhat regularly based on use. Eventually the grit gets clogged or worn too smooth and requires replacing. More aggressive sanding and finer grits wear faster.
While drum sanders utilize quick release clamps for fast belt changes, continually swapping belts contributes added costs. Budgeting for belt supply and spare inventory helps keep the sander running for large workloads. Downtime for belt changes is a maintenance factor as well.
Can Expose Wood Flaws
An additional downside is that drum sanders can potentially cause tear out in wood with knots, flaws, or wild grain. The powerful rotation of the drum pulls out imperfections in some boards more easily compared to hand sanding.
Slower feed rates and inspecting boards helps, but in some cases, drum sanders simply expose flaws other sanding methods may not. Certain boards may require more intermediate steps before drum sanding to prevent marring the surface. It depends on the wood’s properties.
Frequent Small Adjustments Needed
The fast material removal of drum sanders often means you must make many small height adjustments during use. Only removing a 16th of an inch or a few thousandths per pass gives control and prevents over-sanding.
Staying focused on tightening the adjustment a little bit after each pass is key. It’s easy to get distracted and forget to dial down the bed, accidentally removing too much material if you aren’t diligent. The frequent adjustment demands constant attention.
Difficult to Reverse Direction
Once fed into a drum sander in one direction, reversing to sand the other way is problematic. The sanding drum pulls boards from infeed to outfeed only. Turning a board around to run through again takes effort.
Being unable to just run a board back and forth through the sander simply makes the process more cumbersome. For long or heavy boards, the handling difficulties this one-way sanding creates adds time and effort. You need a way to rotate boards.
Key Safety Steps
Operating drum sanders safely requires heightened awareness and precaution. Here are some of the most vital safety measures to take:
- Use push sticks instead of hands for feeding
- Wear eye protection – safety glasses or full face shield
- Ensure dust collection is on and effective
- Tie back hair, remove jewelry/loose clothing
- Check belt tracking alignment frequently
- Provide sturdy infeed and outfeed support
- Remove only very thin amounts per pass
- Maintain focus and avoid distractions
Staying attentive and making drum sander safety a priority is crucial for injury-free operation. Never take shortcuts or operate casually. With proper precautions, drum sanders can be used safely.
Ideal Uses for Drum Sanders
Some of the most recommended uses for drum sanders include:
- Smoothing and flattening wide boards 3”+
- Removing planer marks and defects from rough lumber
- Sanding a slight crown/camber into boards to counteract wood movement
- Leveling and truing up glued panels wider than your planer
- Preparing wide solid wood panels for finishing
- Sanding rows of flooring planks during installation
- Removing old finish and stains from flat boards
Drum sanders excel whenever you need to quickly flatten, smooth, and remove material from wide boards and panels too large for other sanders.
Recommended Grits
The ideal grit depends on your goal:
- Coarse grits (36-60) for heavy stock removal
- Medium grits (80-120) for general smoothing/flattening
- Fine grits (150-180) for final smoothing with minimal scratches
- Extra fine (220+) for abrading and polishing
Start coarser if the board needs significant surfacing, then work finer for polishing. Always sand with the wood grain.
Top Drum Sander Models
Some top drum sander options include:
- JET 22-44 – Popular cast iron benchtop model good for hobbyists
- Powermatic PM2244 – Heavy duty 3HP benchtop model with digital readout
- SuperMax 25-50 – Large combination drum/belt sander able to handle big projects
- Performax 25 x 5 Plus – Powerful industrial 25” drum floor model built for volume
- Laguna 16|32 – High end CNC-control floor standing drum sander with advanced features
- Shop Fox W1713 – Affordable smaller benchtop drum sander good for DIY use
Consider budget, power needs, size constraints, and workload requirements when selecting the right drum sander. Matching the sander to your particular workshop needs ensures the best experience.
Conclusion
Drum sanders provide a huge advantage for rapidly flattening, smoothing, and prepping wide boards well beyond the capacity of other sanders. They can transform rough lumber into polished, finish-ready panels in minutes. However, matching a drum sander to your specific workspace and being aware of the powerful equipment’s safety demands is essential. With good drum sander selection and practices, they can be an invaluable woodworking tool.