Are Planer Blades Universal? [Yes Or No?]
Planer blades are one of the key components of a planer machine. They are responsible for cutting and shaping the wood as it passes through the planer. This leads many woodworkers to wonder – are planer blades universal? Can you use any planer blade in any planer machine? Or do you need to match a specific blade to a specific planer model?
Are planer blades universal? The short answer is no, planer blades are not universally interchangeable between different planer machines.
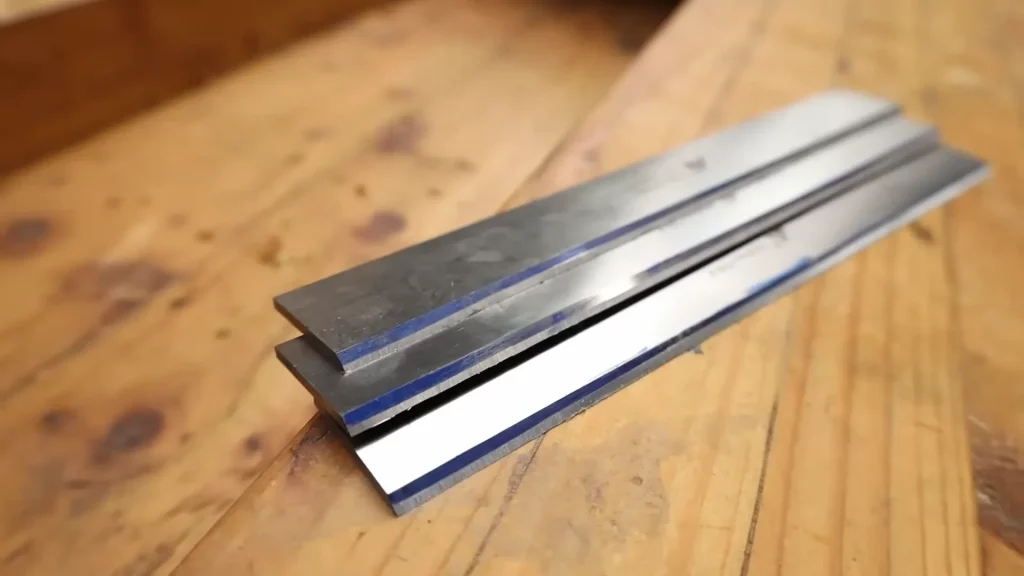
There are several factors that determine planer blade compatibility:
Planer Blade Length
The length of the planer blade must match the length capacity of the planer machine. Planer machines are designed to hold blades of certain maximum lengths. For example, a benchtop planer may only accommodate 12-1/2 inch blades, while a floor standing planer can handle 20 inch or longer blades. You cannot install a 20 inch blade in a planer built for 12 inch blades – it simply won’t fit.
So the first compatibility check is confirming your planer can physically fit the length of blade you have. Many planer manuals will specify what blade lengths it is designed for.
Planer Blade Width
The width of the planer blade must also be compatible with the planer machine. Planers have an opening at the cutterhead that is a certain width – this determines the maximum blade width that can be used.
If you install a blade that is too wide, it will not fit into the cutterhead opening. If you install a blade that is too narrow, it can move side to side in the cutterhead which is unsafe and produces chatter marks.
For example, a common benchtop planer cutterhead width is 3-1/4 inches. So you would need a blade specifically made for 3-1/4 inch planers. Other industrial planers may have wider cutterhead openings that require 4-1/2 inch or wider blades.
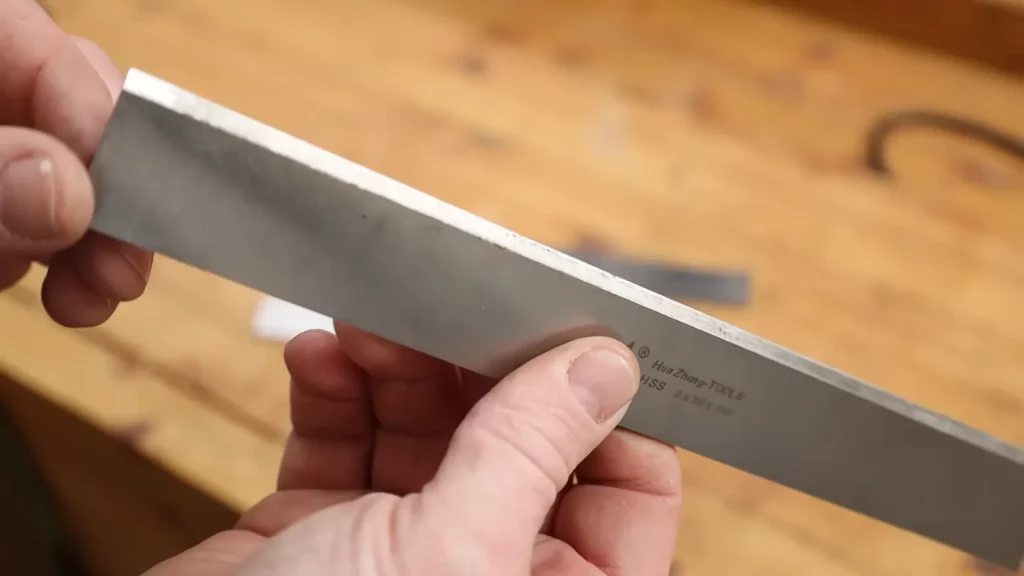
Cutterhead Design
The way the blade mounts to the cutterhead must also match. Planer cutterheads have different designs in terms of how the blades are secured in place.
Some use rectangular blades that are held in place with screws. Others use notched blades that interlock into pockets on the cutterhead. And others use L-shaped blades that wedge into slots on the cutterhead.
So the blade must have the proper shape, notches, holes, etc. to be compatible with the specific cutterhead design. Using a blade designed for a different mounting style simply will not work.
Number of Blades
The number of blades the cutterhead is designed for is also a compatibility factor. Planer cutterheads often need a certain number of blades installed for proper balance and operation.
For example, a cutterhead may be designed for 3 blades spaced evenly around it. You cannot just install 1 or 2 blades – it would be imbalanced. So you need to buy blade sets in the proper quantity for your model planer.
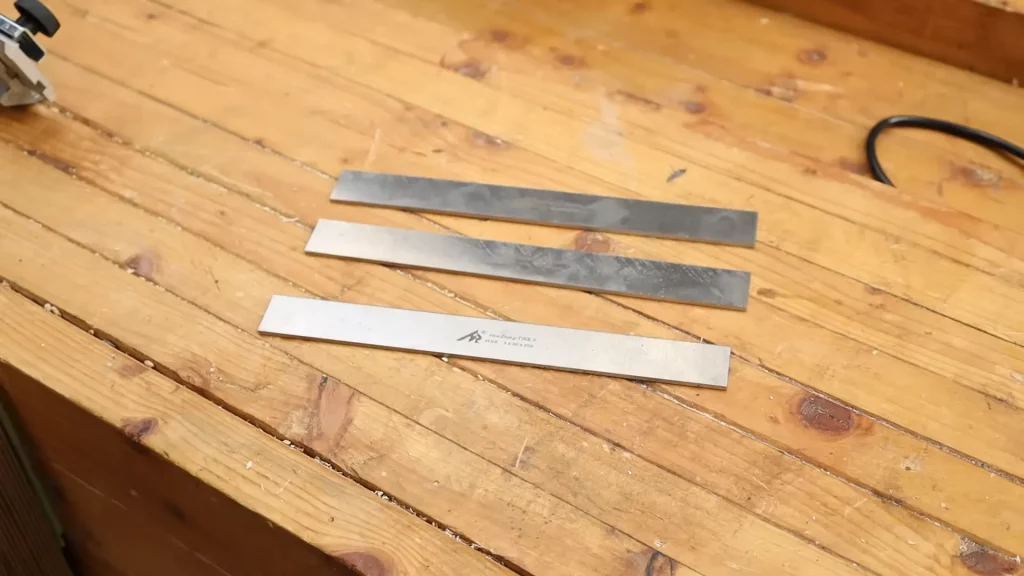
Material and Style of Blade
The blade must also be made of the proper material for your planer. Planer blades are typically made from either high-speed steel (HSS) or carbide. HSS blades hold an edge well but may need occasional sharpening. Carbide blades last longer but are more brittle.
Your planer manual will indicate what style of blade should be used. You should not mix HSS and carbide blades on the same cutterhead, as their cutting properties are different. And the blade bevel angle must match what the cutterhead is designed for – usually 45 or 50 degrees for HSS blades.
Reversible vs. Single-Beveled Blades
Some planers require reversible double-beveled blades, while others are designed for single-bevel blades. Reversible blades can be “flipped” over and used on the opposite cutting edge when one side gets dull. Single-bevel blades are angled on one side only, so the blade must be replaced when that edge is dull.
The cutterhead needs to match the blade type – reversible or single bevel. Mixing them causes uneven cutting. So check your manual for the proper blade style your planer requires.
Aftermarket vs OEM Blades
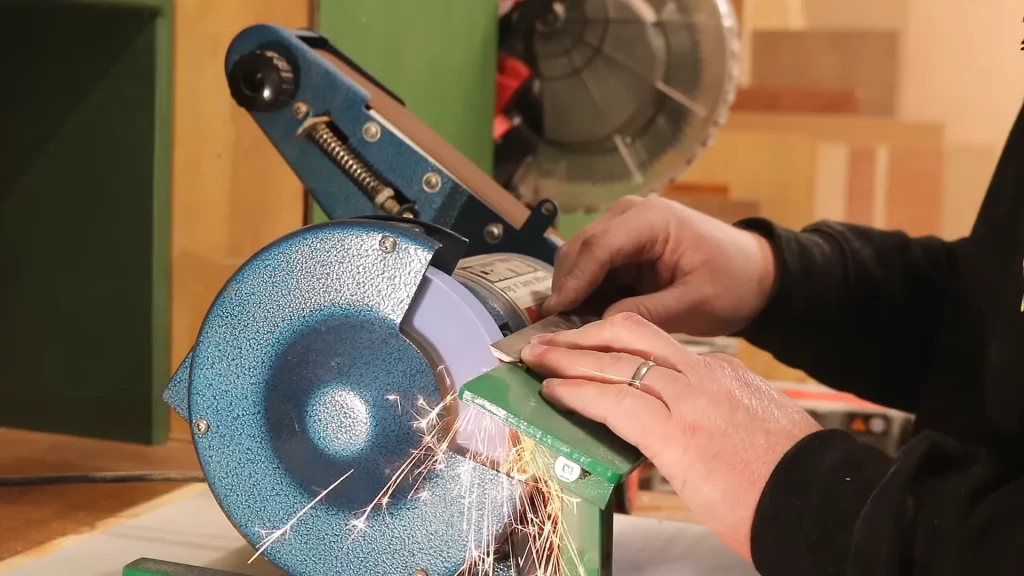
Aftermarket or “universal” planer blade sets are available that claim to be compatible with multiple planer brands. However, it’s usually best to purchase OEM blades made specifically for your planer model.
While aftermarket blades may physically fit your machine, they can sometimes produce vibrations or uneven cutting due to slightly different size tolerances. Genuine OEM blades engineered for your exact planer tend to provide better performance and longer life.
So in summary – while planer blades are not universally interchangeable, if you match all the compatibility factors above – length, width, cutterhead design, quantity, material, bevel style, and OEM fit – you can be assured the blades will properly fit and perform as intended in your specific planer model. Check your planer manual or consult with the manufacturer if you have any doubts about selecting replacement blades. Proper blade selection is key to keeping your planer running safely and achieving smooth, tear-out free cutting.
Types of Planer Blades
There are a few main types of planer blades that may be used depending on the make and model of your planer:
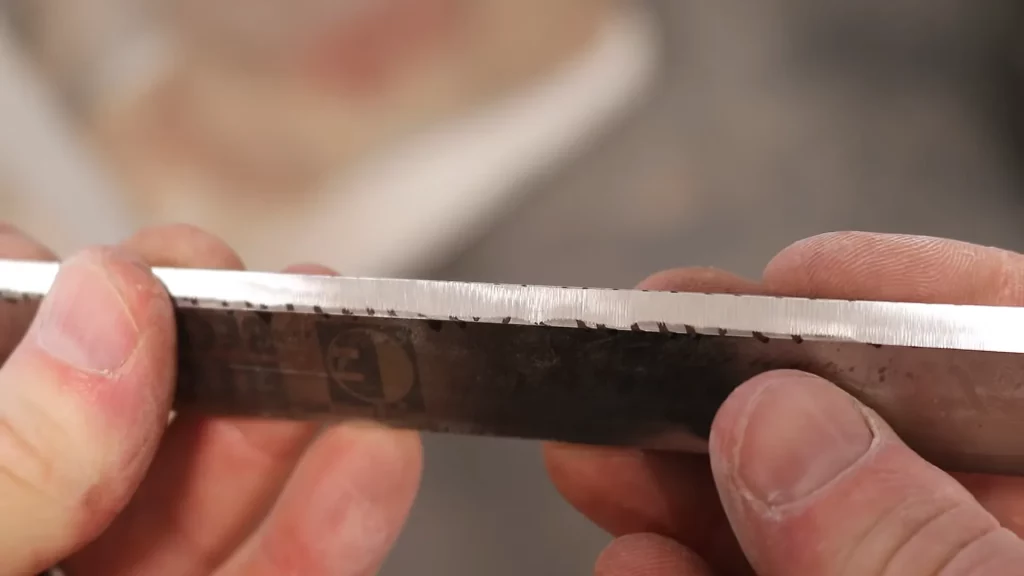
Rectangular Planer Blades
Rectangular planer blades are flat blades that are held in place by screws on the cutterhead. They come in standard widths of 1″, 1-1/4″, 1-1/2″, and 2″ and lengths ranging from 12″ to 27″.
Rectangular blades need to be carefully shimmed and positioned on the cutterhead for proper depth. They also tend to vibrate more than other styles. But they work well for smaller portable planers and are inexpensive and easy to sharpen.
Notched Planer Blades
Notched planer blades have a cut-out notch on the back side that interlocks with ridges on the cutterhead. This helps stabilize the blades and reduce vibrations.
Notched blades are commonly used on larger industrial planers. The notches lock the blades into precise depth settings eliminating the need to shim them. Notched blades provide very smooth cutting performance.
L-Shaped Planer Blades
L-shaped planer blades have an L-profile that wedges into slots on the cutterhead. A locking bar or roller bar then secures the blades in place.
This design is also very effective at reducing vibrations for smooth performance. L-shaped blades are quick to install but more expensive than other styles. They work well in production shop planers that need frequent blade changes.
Reversible Planer Blades
Reversible planer blades are double-beveled so they can be “flipped” and used on both cutting edges. This effectively doubles their life span.
Reversible blades can have either a rectangular or L-shape profile. They work with cutterheads specially designed to support reversible blades. The ability to reuse blades makes them very cost effective.
Disposable Planer Blades
Disposable planer blades are single-beveled blades that are designed to be thrown away and replaced when dull. They cannot be sharpened or reversed.
Disposable blades are mostly used in portable benchtop planers. Their simple design makes them inexpensive and easy to swap out. But frequent blade replacement can add up in cost over time versus resharpenable blades.
Knowing the different types of common planer blades can help you choose the optimal design for the kind of planering work you need to accomplish. Refer to your planer manual for exactly which style of blade your model requires.
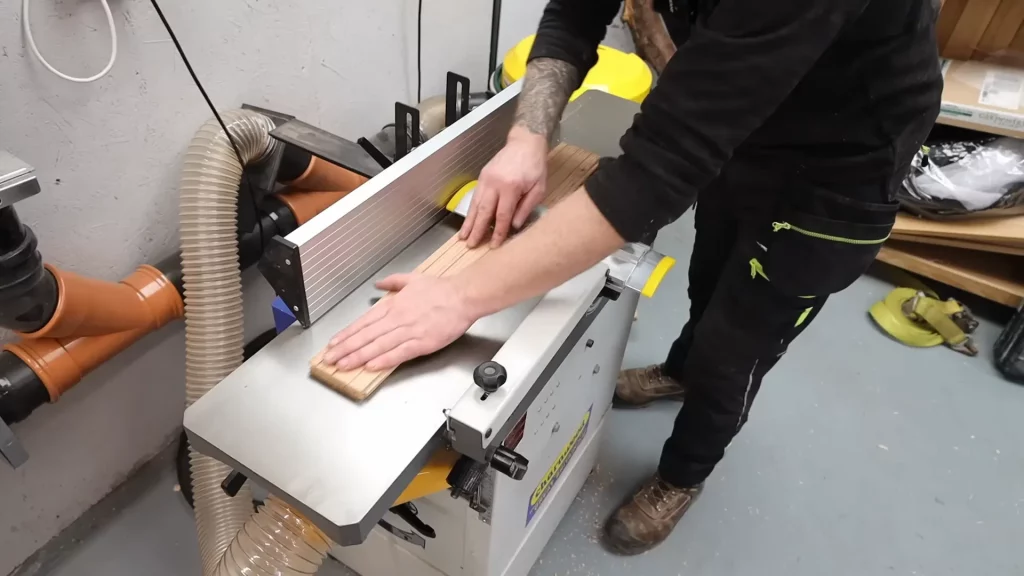
Planer Blade Parts
Planer blades have just a few main parts, but understanding the function of each is helpful for properly maintaining your blades:
Cutting Edge
The cutting edge is the beveled part of the blade that shears and cuts the wood fibers as material passes by. It’s the sharpened edge that removes material.
Keeping the cutting edge sharp is critical for proper planing. A nicked, warped, or dull cutting edge will tear wood fibers rather than making smooth cuts. Regular inspection and sharpening helps prolong the life of the cutting edge.
Body
The body is the main plate of the blade that provides structural support. It’s the part that mounts to the cutterhead. The quality of the blade body material – typically high-speed steel or carbide – impacts its durability and lifespan.
Cracks or deformation in the body can lead to vibration and uneven cuts. A quality blade body withstands wear well even under heavy use.
Beveled Edge
The beveled edge is the angled slope cut into the body of the blade which forms the cutting edge. Common bevel angles are 45 and 50 degrees, depending on the blade.
Maintaining the proper bevel angle is important when sharpening the blade. If the bevel angle changes, it alters the orientation of the cutting edge and affects performance.
Mounting Holes
Mounting holes refer to the holes or notches in the blade body that allow it to be mounted on the cutterhead.
These may be threaded holes to accept screws, notches that fit over ridges, or openings that slide over mounting bars depending on the style of blade. Proper positioning in the mounting holes ensures the blade sits at the intended height.
Anti-Kickback Features
Some planer blade styles have anti-kickback features – small serrated points near the cutting edge. These serrations score the wood fiber to help prevent kickback of stock as it passes the cutterhead.
The points need to be kept sharp along with the cutting edge for maximum anti-kickback effectiveness and safety. Rounded-over points lose their ability to score the wood properly.
In summary, understanding each part of the planer blade helps ensure proper use and maintenance for optimal cutting performance and longer blade life. Keeping the cutting edge sharp, maintaining sturdy blade bodies, and securing blades properly in the mounting holes are key for smooth planing results.

Blade Care & Maintenance
Proper care and maintenance is essential for planer blades to have a long usable lifespan:
Keep Blades Sharp
Sharpen blades regularly to maintain a keen cutting edge. Nicked, rounded, or dull edges will tear wood fibers rather than slicing them cleanly.
HSS blades can be sharpened yourself with a grinding wheel or sharpening jig. Carbide blades need to be resharpened professionally. Follow the manufacturer’s sharpening instructions.
Use Blade Guides
Adjust blade guides closely to the workpiece to provide backing support as it passes the cutterhead. This prevents thin edges from vibrating or tearing out.
Guides should be within 1/16″ of the stock thickness. Loosen and slide guides into position for each workpiece.
Wax Tables Frequently
Apply paste wax to infeed/outfeed tables every few uses. This helps reduce friction so workpieces move across the tables smoothly without sticking.
Less resistance means the cutterhead doesn’t have to work as hard and blades stay sharper longer. Keep tables rust-free as well.
Rotate Blades Periodically
Rotate blades to distribute wear evenly. The same blades always cut the same section of workpiece. Rotating evens out the wear for maximum life from the full set of blades.
Stagger and reposition blades every 5-10 sharpenings for uniform cutting. Follow manufacturer’s instructions.
Clean Chips Frequently
Remove wood chips and dust from around cutterhead regularly to prevent buildup. Clogged chip extraction ports lead to jams that overload blades unevenly.
Blow out dust after every use. Clean any packed sawdust from inside planer body as needed to maintain good chip flow.
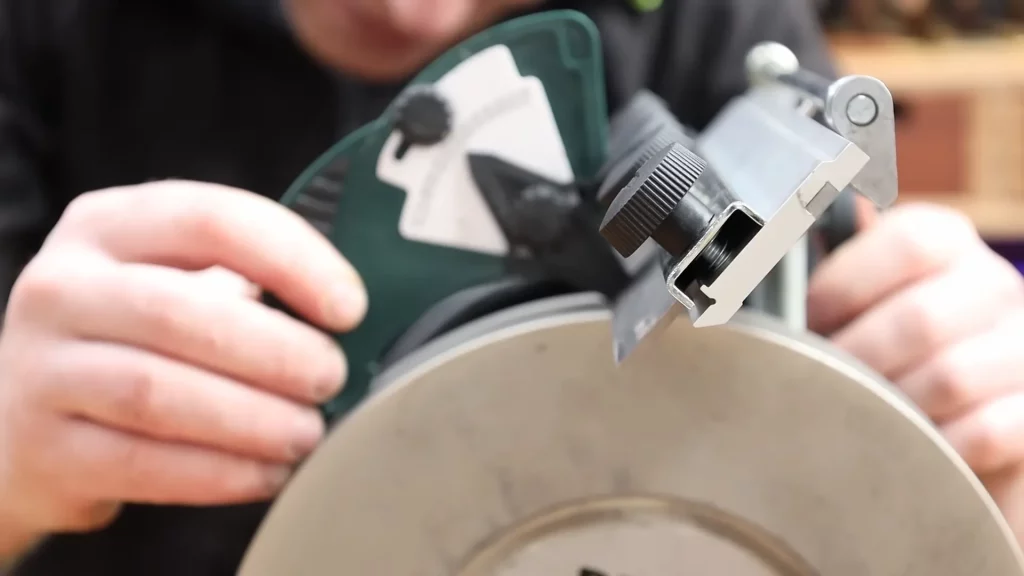
Check/Replace Drive Belts
Inspect drive belts and replace belts periodically to ensure optimal power transfer to cutterhead. Slipping belts reduce cutting speed and performance.
Re-tension or replace belts displaying cracks, glazing, or signs of wear per manufacturer’s guidance.
Proper planer blade care results in blades that cut accurately and smoothly for years of use. It also improves safety by reducing tearing, kickback risks, and cutterhead jams. Invest a few minutes after each use and enjoy better planing results.
Signs It’s Time to Replace Planer Blades
Even with good maintenance, planer blades gradually wear out over time. Here are signs it may be time to install new blades on your planer:
Tear-Out on Edges
If you notice fuzz, splintering, or tear-out along the edges or surface of workpieces, the cutting edges are likely dull or nicked.
Sharpening may help, but if damage is too deep, new blades will be needed to restore clean cuts.
Blade Chatter or Vibration
Excess vibration during planing can indicate blades are warped, damaged, or need sharpening. Continued use while vibrating risks blade breakage or cutterhead damage.
Rotating blades can help isolate a bad one. Otherwise replace the full set for smooth, quiet cuts.
Noticeable Grooves in Wood
Over time, worn blades form visible grooves across the wood surface rather than making clean, even cuts. The cutting edges are rounded over and are tearing at the wood.
Replacing blades will restore flat, consistent planing. Check for proper blade depth adjustments as well.
Diminishing Cut Depth
When planed boards start coming out thinner than the depth setting, it likely means the blades are too short from repeated sharpening.
The cutting edges no longer protrude enough to make full-depth cuts. New, full-length blades are needed.
Excess smoke or resin buildup
Smoke coming from the cutterhead and sticky resin deposits are clues blades are overheating from friction and getting dangerously dull. Using them like this risks cutterhead damage.
Don’t delay – dull blades need sharpening or replacement ASAP. Slow feed rate if overworking them.
Be alert for these signs your planer is ready for new blades. Continuing to use overly worn blades may lead to injury as well as poor performance. Invest in quality replacement blades to renew your planer’s cutting effectiveness.
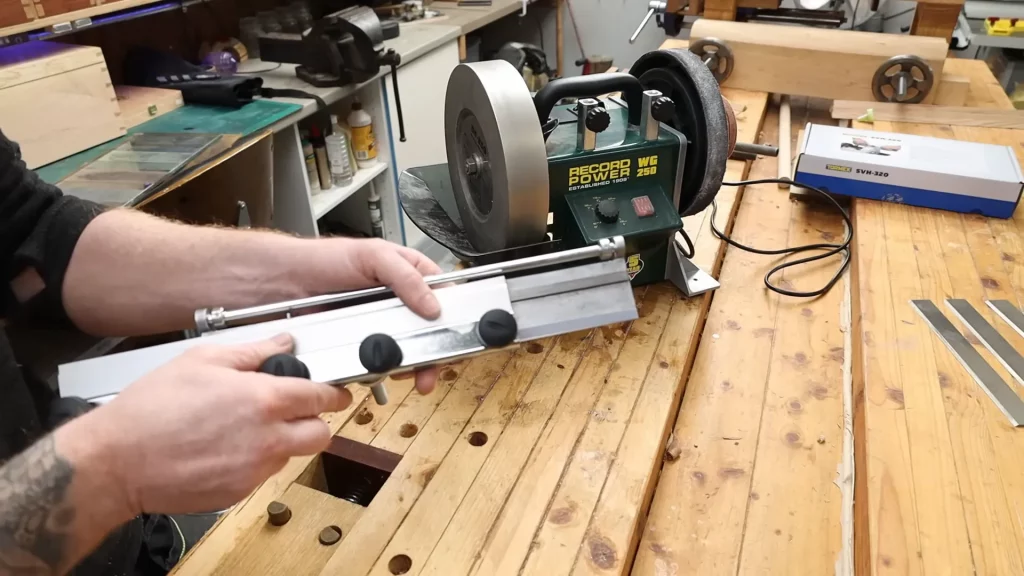
Planer Blade Safety Tips
Working with planer blades involves some risks. Follow these safety tips when handling planer blades:
Use Thick Work Gloves
Wear sturdy work gloves when handling planer blades to protect your hands. Blades are extremely sharp and can easily cause deep cuts.
Leather gloves provide the best protection when installing and removing blades from the cutterhead.
Secure Blades Before Servicing
Always switch planer OFF and disconnect power before blade maintenance. Lock cutterhead using manufacturer’s instructions so it can’t turn.
Attempting to service blades while they can still spin is very hazardous. Make blades are fully secured first.
Keep Blades Covered
Place removed blades immediately into a protective cover or sheath to shield the sharp edges. Never carry or set bare blades down.
Covers prevent accidents between uses. Store blades safely in a drawer, cabinet, or rack when not in use.
Tighten Blades Evenly
When installing new blades, progressively tighten mounting screws in a crisscross pattern. This avoids putting uneven stress on the cutterhead.
Follow torque specs in manual. Improperly mounted blades can vibrate loose during use.
Use Push Sticks
Always use push sticks to feed stock through planer, keeping hands well clear of the cutterhead. Never reach into cut zone.
Push sticks prevent accidental contact with spinning blades that can cause horrific injuries.
Stay alert and use extreme caution when maintaining planer blades. Their exposed cutting edges pose risks if mishandled. But following sensible safety practices helps ensure safe, trouble-free performance.
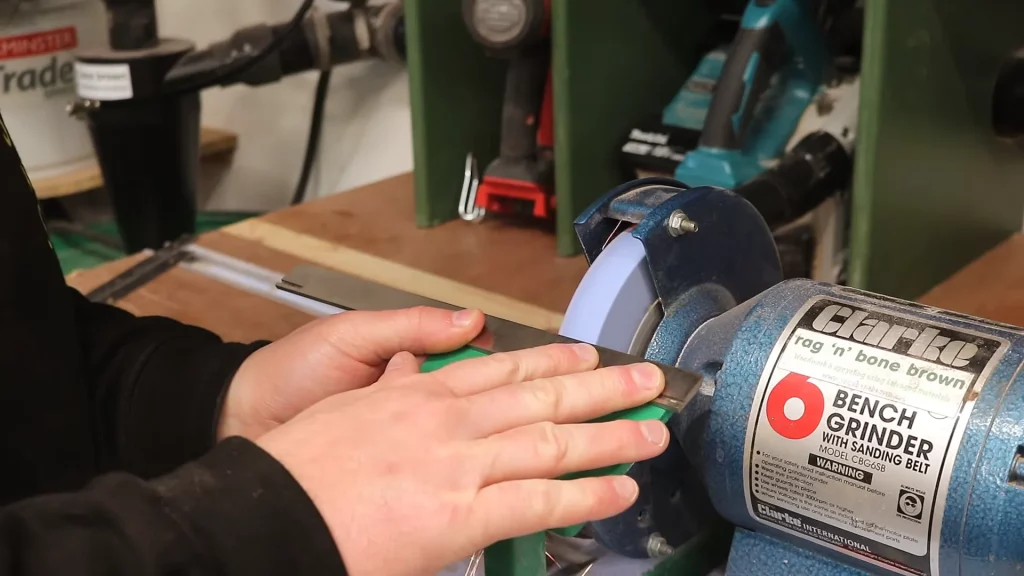
Choosing Planer Blade Materials
Two main types of materials are used to manufacture planer blades:
High Speed Steel (HSS)
High speed steel (HSS) is a hardened steel alloy that maintains a very sharp edge but is softer and more impact-resistant than carbon steel. HSS blades stay sharper longer than carbon steel and are easier to sharpen.
HSS is a good economical choice for portable planers used intermittently by woodworkers and DIYers. HSS blades can be sharpened several times before needing replacement.
However, industrial shops that use planers heavily generally prefer carbide blades since HSS requires more frequent sharpening or replacement under high-use conditions. But for light to moderate use, HSS provides an affordable and long-lasting blade option.
Carbide
Carbide-tipped planer blades have hard carbide inserts along the cutting edge which stay sharper much longer than standard HSS blades. Carbide holds its edge up to 15x longer than HSS before needing sharpened.
This makes carbide blades ideal for industrial/production shops running planers daily for many hours. Fewer sharpenings and blade changes mean higher productivity. The downside is carbide blades have a higher upfront cost.
However, their extended lifespan means over time the cost per use is lower than disposable HSS blades. Many serious woodworking shops also employ carbide blades to reduce planer downtime. Carbide blades require special professional sharpening but produce minimal tear-out even when heavily used.
For very high-volume planing work, carbide tipped blades are recommended. Their longevity offsets the initial price. For light use, economical HSS blades are often the better choice. Consider your usage level and shop budget when deciding on planer blade materials.
The Bottom Line
The bottom line is that planer blades are generally not universal or interchangeable between different planer models and brands. There are several critical factors that determine planer blade compatibility:
- Blade Length – Must match planer’s maximum cutting width capacity
- Blade Width – Must fit cutterhead opening exactly
- Cutterhead Design – Blade must match mounting method (screws, notches, etc)
- Number of Blades – Cutterhead requires specific quantity for balance
- Blade Bevel – Angle must match cutterhead specs (typically 45 or 50 degrees)
- Blade Type – Cutterhead designed for reversible or disposable blades
- Quality – OEM blades engineered for specific planer model typically perform best
While aftermarket “universal” blades may physically fit into a planer, they often don’t result in optimal performance and longevity compared to blades designed specifically for that make and model.
Questions We Have Covered In This Article:
Here are some of the key questions specifically related to planer blade universality that were covered in the article:
- Are planer blades one standard size that fits all planer models?
- What blade dimensions like length and width must match the planer?
- How does the cutterhead design affect blade compatibility?
- Does the quantity of blades matter for proper balance?
- What’s the difference between reversible and disposable planer blades?
- Do the bevel angle and blade materials need to match the planer?
- Are aftermarket “universal” blades a good substitute for OEM blades?
- Can you use jointing planer blades in a benchtop planer and vice versa?
- Will narrow planer blades work in a wider planer and leave clean edges?
- Can you mix carbide and steel blades on the same cutterhead?
- How do you look up the proper replacement blades for your specific planer?
- What problems can occur if incorrect blades are installed in a planer?
- How can you identify when blade compatibility issues are causing poor planing performance?
The article explains in detail why planer blades are generally not interchangeable between different makes and models. The key is matching all the critical specifications of the blades to the design of the cutterhead and planer itself. This ensures smooth, accurate cuts and trouble-free planing.