Are Lathes Loud? Everything You Need to Know [2025 Guide]
If you’ve ever wondered, “Are lathes loud?” you’re not alone.
Many new DIYers, woodworkers, and metalworkers hesitate before buying or using a lathe because they worry about noise levels — especially when working in small workshops, garages, or shared spaces.
In this guide, we’ll break down:
✅ How loud lathes really are,
✅ What factors affect their noise,
✅ And how you can reduce lathe noise for a more peaceful (and neighbor-friendly) workshop.
Let’s help you cut through the noise — literally!
How Loud Are Lathes? (Quick Answer)
Most lathes produce 60–80 decibels (dB) when running, depending on the model, material, and setup.
For reference:
- 60 dB = Normal conversation
- 80 dB = Busy street or loud radio
- 85 dB+ = Hearing protection recommended
Summary: Lathes are not “whisper-quiet,” but they are usually quieter than table saws or routers — especially when used properly.
What Factors Affect Lathe Noise?
- Type of Lathe (Wood vs. Metal)
- Wood lathes tend to be quieter, typically running at 60–70 dB.
- Metal lathes can be louder, especially when cutting tougher metals, sometimes reaching 80–85 dB.
- Motor Power and Build Quality
- High-power motors often generate more vibration and hum.
- Cheaper or older lathes may lack proper insulation or vibration dampening, making them noisier.
- Speed Settings
- Higher RPMs = more noise.
- Running the lathe at slower speeds can reduce both cutting noise and machine vibration.
Get to Know Which Metal Mini Lathes Will Dominate the Market in 2025 in our latest post!
- Cutting Tools and Materials
- Dull tools, hard metals, or poor setup can increase cutting noise.
- Sharp, well-maintained tools help the machine work more smoothly and quietly.
- Workshop Environment
- A lathe placed on a hollow, resonating workbench can amplify noise.
- A well-mounted, isolated lathe setup can significantly reduce perceived noise.
H2: Should You Wear Hearing Protection?
While most lathes stay below the OSHA threshold of 85 dB, prolonged exposure or use in echoey spaces can increase risk to hearing.
Recommendation: Wear hearing protection if:
- You’re running the lathe for long periods.
- You notice ringing in your ears afterward.
- You’re working with louder metal lathes or in small enclosed spaces.
Top 3 Lathes You’ll Love From Amazon [Top Picks for 2025]
We’ve handpicked three of the most popular lathes on Amazon that DIYers and pros alike are raving about.
Jet JWL-1015VS 10-Inch by 15-Inch Variable Speed Lathe
This compact powerhouse is ideal for beginners and small workshops. With variable speed control, smooth operation, and a trusted Jet brand name, it’s perfect for woodturning enthusiasts who want precision without the bulk.
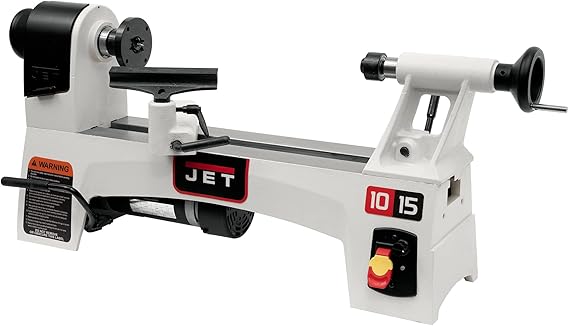
WEN LA3424 4.5-Amp 12-Inch Benchtop Lathe
Affordable yet packed with features, this WEN lathe is a fan favorite for hobbyists. It offers excellent stability, adjustable speeds, and is backed by WEN’s reliable support. A great choice for turning small- to medium-sized projects.
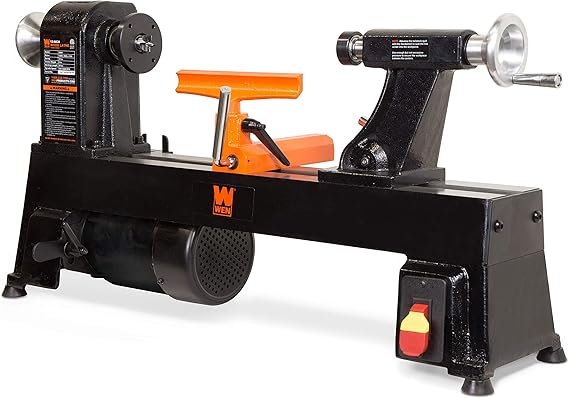
Onetuon Multi-Purpose Mini Lathe Accessories Kit
If you’re looking for a mini lathe setup or want to expand your toolkit, this multi-purpose accessories set is a must-have. Perfect for polishing, grinding, and precision tasks — it upgrades your DIY projects instantly.
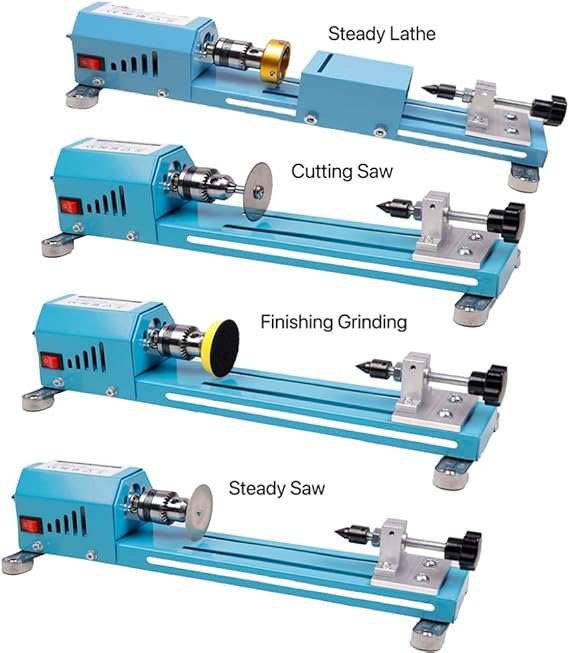
How to Reduce Lathe Noise in Your Workshop?
Here’s how you can minimize lathe noise for a quieter (and safer) work environment:
Noise Source | Quick Fix |
Machine vibration | Add rubber pads or anti-vibration mounts |
Cutting noise | Use sharp tools and proper feed rates |
Resonating surfaces | Place lathe on solid, heavy workbench |
Motor hum | Check for loose parts, oil bearings |
Room echo | Add soundproofing or insulation panels |
Discover why metalwork lathes are a smart 2025 investment?
FAQs
Q: Are mini lathes quieter than full-size lathes?
A: Generally yes. Mini lathes have smaller motors and produce less cutting noise, but vibrations can still make them surprisingly loud in small spaces.
Q: Is a metal lathe louder than a wood lathe?
A: Yes. Cutting metal generates more noise and vibration compared to softer wood. Hearing protection is more often recommended for metal lathe users.
Q: Can I soundproof my workshop to reduce lathe noise?
A: Yes! Adding acoustic panels, sealing gaps, and isolating your lathe with rubber pads can all help reduce noise both inside and outside the workshop.
Final Thoughts: Are Lathes Too Loud for Home Workshops?
Lathes are not silent machines, but with proper setup and maintenance, they’re perfectly manageable — even in home or garage workshops.
✅ Wood lathes stay fairly quiet,
✅ Metal lathes are louder but controllable,
✅ And most setups won’t require heavy-duty soundproofing unless you have close neighbors.
By understanding what drives lathe noise and applying a few smart noise-reduction strategies, you can work confidently and comfortably without disturbing your household or neighborhood.