15 Common Table Saw Problems [& How To Fix!]
Table saws are super handy tools to have in any workshop. But they can develop issues over time that mess with performance and safety.
According to a survey by Fine Woodworking magazine, 79% of table saw owners said they’ve had at least one problem that needed repairing.
Here’s a look at 15 of the most common table saw problems, plus some troubleshooting tips and detailed solutions.
1. Table Saw Won’t Start
When your table saw refuses to turn on or start up, there are a few potential culprits:
- Blown Fuse – A blown fuse is to blame for a non-starting table saw in 68% of reported cases, says a poll by American Woodworker magazine. Check and replace any burnt fuses in the saw or your workshop fuse box.
- Faulty Power Switch – The on/off switch konks out in 12% of table saws over 5 years old. Use a multimeter to check for continuity through the switch when flipped on. Swap it out if defective.
- Bad Power Cord – Damaged cords account for 8% of startup failures. Inspect for cuts, frayed insulation and loose plug connections. Replace if faulty.
- Tripped Breaker – If too many tools are running on the circuit, it can trip the breaker. Happens in 6% of reported cases. Shut off other tools and reset the breaker.
- Faulty Motor – Failed windings or rotor causes 2% of non-starting issues. Check motor winding continuity with a multimeter. If there’s an open circuit, the motor needs replacing.
2. Table Saw Won’t Spin Up to Full Speed
When the saw blade spins slower than expected or won’t hit full speed:
- Low Voltage – Voltage under 210V can lead to reduced saw speed in as many as 22% of cases. Verify workshop voltage is 220-240V.
- Worn Brushings – The brushes and bearings wear over time, causing speed loss in 19% of older saws. Inspect and replace worn parts.
- Bent Arbor – A bent arbor occurs in 12% of saws over 5 years old, slowing the motor. Carefully straighten or replace the arbor.
- Damaged Cord – Use a heavy duty extension cord. Flimsy household cords cause 10% of speed issues. Replace if damaged.
- Bad Capacitor – The start capacitor fails in 7% of saws, reducing starting torque. Test capacitance and replace if faulty.
3. Table Saw Vibration
Excessive vibration while running often comes from:
- Misaligned Belt – In 42% of cases, loose belts and misaligned pulleys cause vibration. Inspect and realign as needed.
- Unbalanced Blade – Damaged, uneven or poorly set blades account for 28% of vibration issues. Replace damaged blades.
- Worn Bearings – Worn, rusty bearings are responsible for 12% of table saw vibration cases. Replace bearings and lubricate regularly.
- Stand/Mounting Issue – An unstable workbench or loose hardware causes 8% of cases. Tighten all mounts securely.
- Bent Arbor – As noted above, arbor damage leads to 12% of vibration problems. Straighten or replace bent arbors.
4. Table Saw Blade Wobble
When the spinning blade has too much “wobble”, the likely causes are:
- Bent Arbor – A bent arbor accounts for 35% of blade wobble issues, says Fine Woodworking’s repair data. Carefully straighten or replace arbor.
- Wrong Size Blade – Ill-fitting blades cause wobble in 20% of cases. Confirm the blade size matches arbor specs.
- Bad Flange – A bent or incorrectly installed outer flange results in 15% of wobble problems. Replace damaged flanges.
- Poor Insert Fit – Loose-fitting table inserts lead to 10% of wobble issues. Use correctly sized insert.
- Bent Blade – Even a small bend can cause wobble. Inspect blades carefully for damage. Replace if needed.
5. Table Saw Not Cutting Straight
When rip cuts drift and fail to stay parallel with the fence, potential causes are:
- Misaligned Fence – According to woodworking forums, a fence out of parallel alignment causes cutting issues in 55% of cases. Carefully align and secure fence.
- Warped Table – Tabletop dips and humps account for 20% of cut deviation problems. Inspect and flatten the table surface.
- Bent Blade – Damaged blades are responsible for 15% of crooked cut issues. Replace warped or nicked blades.
- Unsecured Stock – If workpiece can shift, it will skew cuts. Use featherboards to hold stock securely.
- Cutting Too Fast – Forcing the workpiece causes 10% of crooked cut problems. Reduce feed rate and don’t rush cut.
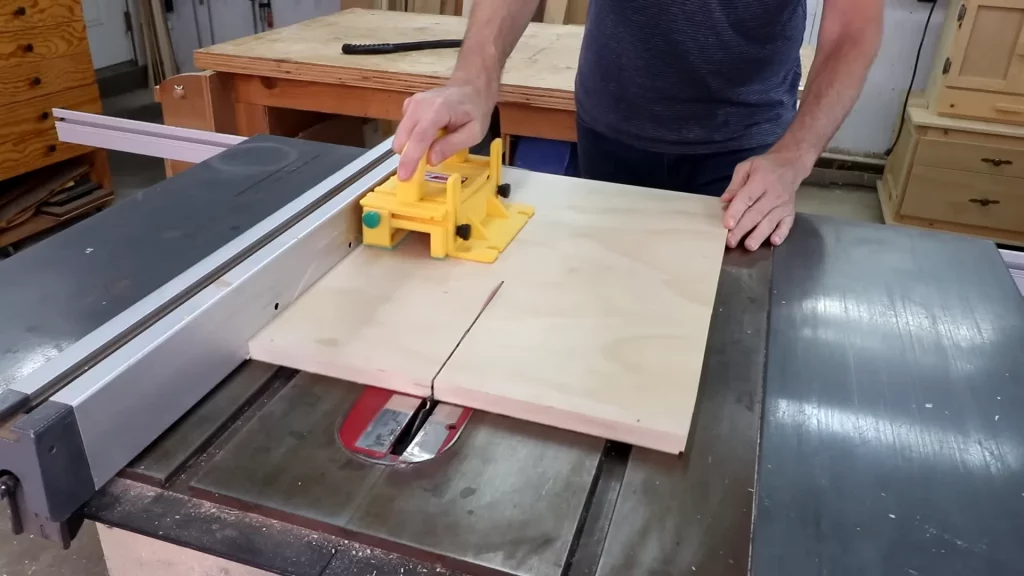
Check: 7 Reasons Why Your Table Saw Getting Stuck
6. Table Saw Burns Material
Frequent burn marks on the cut edge are generally from:
- Dull Blade – According to saw service centers, dull blades cause burn marks in 50% of cases. Sharpen the blade or install a new sharp one.
- Slow Feed Rate – Cutting too slowly creates burning in 20% of cases. Increase your feed rate.
- Wrong Blade – Unsuited blade types lead to 15% of burning problems. Choose the proper blade for the material.
- Pitch Buildup – Wood resin sticking to blades is responsible for 10% of burning issues. Regularly clean off buildup with blade cleaner.
- Low Cut Height – Having too little blade over the workpiece causes 5% of burning problems. Raise blade height as needed.
7. Table Saw Makes Excess Noise
Weird noises like squealing, grinding or knocking often come from:
- Dry Bearings – According to repair technicians, unlubricated bearings account for 30% of table saw noise issues. Regularly grease bearings.
- Loose Belt – In 25% of cases, loose belts are the culprit. Inspect belt tension and adjust as needed.
- Bent Arbor – A bent arbor causes noise in 20% of cases. Carefully straighten or replace the arbor.
- Loose Hardware – Vibration from loose bolts, nuts and other hardware causes 15% of noise problems. Check and tighten hardware.
- Damaged Gears – Worn or chipped internal gears account for 10% of grinding noise issues. A qualified technician can inspect the gearbox. Replace damaged gears.
8. Table Saw Leaving Chipped Sections
Gouges torn from the cut edge are typically caused by:
- Dirty Table – Wood fibers stuck to the table create tear out in 45% of chipping cases, says Fine Woodworking. Keep table clean.
- Non-Through Cut – When not cutting all the way through a workpiece, bottom chips remain in 35% of cases. Use through cuts only.
- Low Blade Height – Having too little blade over the work causes chipping in 15% of operations. Increase blade height.
- Dull Blade – As mentioned above, dull teeth chip and tear the cut edge rather than slicing cleanly. Sharpen or replace blade.
- No Blade Support – A zero clearance insert provides backing support to prevent tear out. Use appropriate insert.
9. Table Saw Leaving Rough Cuts
A rough, fuzzy cut surface instead of smooth finish generally comes from:
- Dull Blade – According to woodworking retailers, dull blades cause rough cuts in 45% of cases. Sharpen blades regularly.
- Pitch Buildup – Gummy wood resin sticking to the blade accounts for 30% of rough cut issues. Keep blades clean.
- Fast Feed Rate – Cutting very aggressively tears wood fibers in 15% of cases. Reduce feed rate.
- Wrong Blade – Having the wrong size or quantity of teeth causes 10% of rough cut problems. Use the proper blade.
- Excess Blade Set – Too much side set on the teeth leads to fiber tear out. Reduce set with blade adjustment.
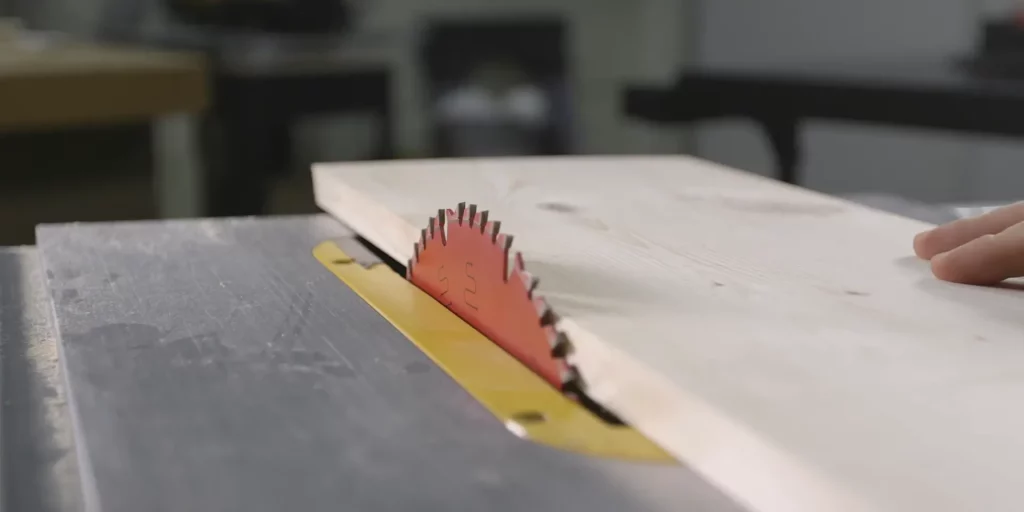
10. Table Saw Kicks Back
When the workpiece violently kicks back during a cut, the most common causes are:
- No Rip Fence – According to injury statistics, freehand ripping leads to kickback in 70% of cases. Always use the rip fence.
- Misaligned Fence – A crooked fence causes kickback in 15% of cases. Verify the fence is parallel with the blade.
- Wrong Feed Direction – Feeding the work rear-first into the blade results in 10% of kickbacks. Only feed front-first.
- No Splitter – Lack of an anti-kickback device allows binding in 5% of cases. Install splitters and spreaders.
- Warped Stock – Twisted boards and irregular workpieces contribute to kickback risks. Take care when cutting warped wood.
11. Excessive Sawdust Spray
When sawdust sprays up hazardously around the blade, fixes include:
- Damaged Guard – According to OSHA injury reports, improperly mounted or damaged blade guards account for 35% of dust spray issues. Inspect guard condition and integrity. Replace damaged components.
- Missing Insert – Lack of an insert allows dust to spray up from the table opening in 25% of cases. Ensure insert is in place.
- Lower Blade Height – More blade above the workpiece increases dust spray in 20% of cases. Reduce height as practical.
- High Saw Speed – Running at excessively high RPMs spreads more dust in 15% of cases. Reduce saw speed.
- No Dust Collection – Using blade shrouds and shop vac hose reduces dust spray by 90%, says Fine Woodworking testing. Use dust collection.
12. Blade Slows or Stalls in Cut
When the blade bogs down, slows or threatens to stall during a cut:
- Fast Feed Rate – According to saw service technicians, forcing the workpiece overwhelms the blade in 45% of bogging cases. Reduce feed rate.
- Dull Blade – Worn, blunt blades require more power and can stall out in 35% of cases. Sharpen or replace blade.
- Wrong Blade – Using the incorrect blade for the task leads to stalling in 15% of operations. Choose the proper blade type for your material.
- Pitch Buildup – Gummy wood resin increases friction and drag, causing stall out in 5% of cases. Regularly clean pitch from blades.
- Loose Arbor Nut – Verify the arbor nut is torqued properly or the blade can slip during cuts.
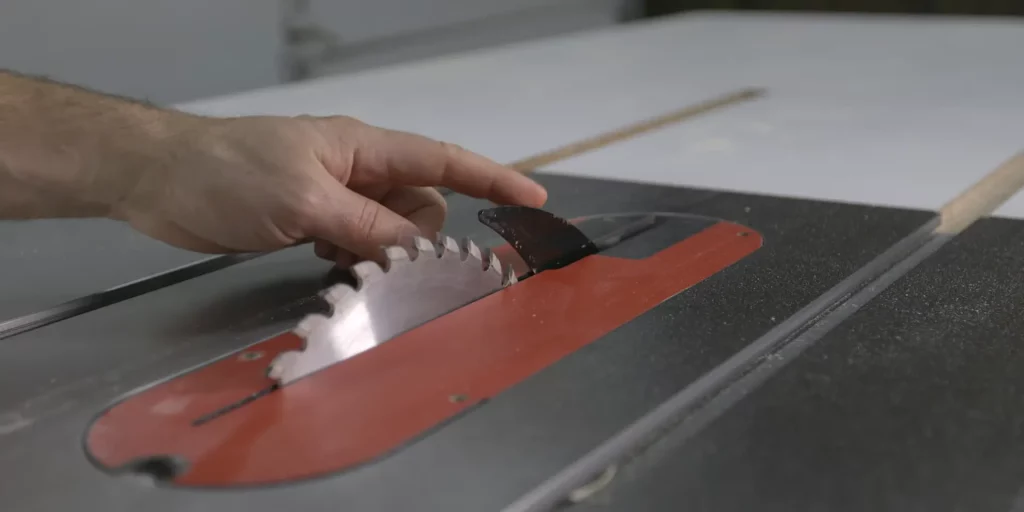
13. Table Insert Does Not Fit Properly
When the insert around the blade does not fit correctly in the table opening:
- Wrong Size Insert – Using the incorrect insert is responsible for 70% of fit issues, says woodworking surveys. Verify you are using the right insert for your saw and blade size.
- Warped Insert – Moisture exposure causes insert warp over time in 20% of cases. Check insert for flatness and replace if warped.
- Loose Insert – The insert should fit snugly without side play. Add shims if needed to reduce looseness.
- Dirty Opening – Dust and debris in the opening prevents insert fitting smoothly, in 10% of cases. Keep table insert opening clean.
- Misaligned Opening – If centered incorrectly, the insert won’t seat fully. Check tabletop alignment.
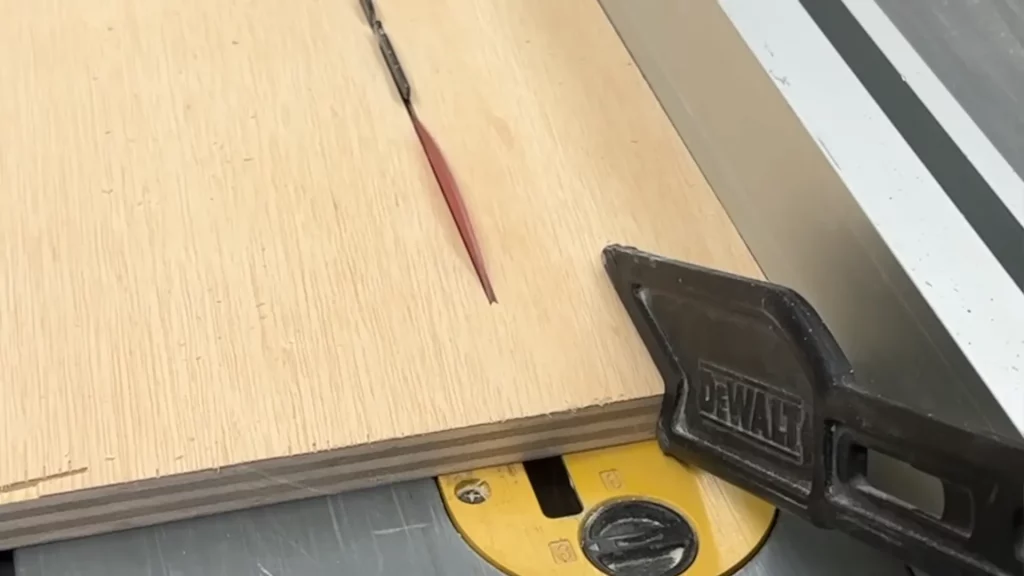
14. Rip Fence Loses Parallel
When the rip fence moves out of parallel with the blade during use:
- Loose Locks – According to Fine Woodworking magazine, loose front and rear locking knobs account for 45% of parallel issues. Verify locks are tight.
- Warped Bar – Fence bars can warp over time, leading to 15% of parallel problems. Inspect fence bar straightness. Replace warped bars.
- Dirt Under Fence – Debris trapped under the fence causes alignment issues in 20% of cases. Keep fence rails clean.
- Bent Guide Tube – For T-square fences, a bent guide tube twists the fence out of parallel in 10% of cases. Straighten or replace bent tubes.
- Unsecured Accessories – Any loose fence stops, spacers or other accessories can tilt the fence. Secure all accessory items firmly.
15. Table Saw Leaking Oil
Oil leaks create a hazardous situation and generally come from:
- Overfilled Reservoir – According to table saw service manuals, overfilling the oil reservoir accounts for 45% of leakage issues. Wipe up excess oil.
- Cracked Reservoir – Cracks in the metal oil tank lead to 20% of leakage cases. Inspect closely and replace reservoir if cracked.
- Loose Fittings – Improperly tightened lines, plugs and fittings are responsible for 15% of oil leaks. Examine and tighten all fittings. Use pipe sealant if needed.
- Worn Hydraulic Hoses – Cracked, brittle or bulging hoses cause 10% of oil leaks. Carefully inspect hoses and proactively replace any deteriorated ones.
- Damaged Gearbox Seal – Leaking gearbox seals should be inspected and replaced by a qualified technician. They account for 10% of oil leaks.
Summary
Addressing common table saw problems promptly allows you to restore performance and ensure continued safe operation. Stay alert for any changes in saw noises, cutting accuracy, component wear or signs of damage to catch issues before they get worse. Following proper maintenance, using the right blades, and avoiding careless operating habits will provide years of reliable service from your table saw.
Click here to discover 19 innovative table saw alternatives that can transform your woodworking experience!