11 Common Delta Planer Problems [Easy Fixes!]
A perfectly tuned delta planer can produce glassy smooth wood surfaces ready for finishing.
But over time, issues like snipe, tearout, rough finishes, and chatter can arise to hamper results.
Diagnosing and fixing common delta planer problems keeps your planer performing at its best for years.
In this guide, we’ll explore the eleven most common issues woodworkers encounter with their delta planers.
From knife maintenance to stabilizing boards through the cut, we’ll cover symptoms, causes, and solutions for problems like snipe, chip marks, blade vibration, stalling, and uneven planing depth.
With a bit of troubleshooting and maintenance knowledge, you can get your planer back up and running quickly when problems pop up.
Read on to learn how to identify and address the eleven most common delta planer problems.
Snipe
Snipe is one of the most frustrating delta planer problems. It refers to deeper cuts at the beginning or end of a board as it passes through the planer. This leaves gouges or indentations that ruin an otherwise smoothly planed surface.
Symptoms:
- Gouges or deeper cuts at the leading or trailing edge of boards
- Grooves that run along the length of the board at the beginning or end
Causes:
- Feed rollers are worn or misaligned
- Outfeed table is set too low
- Wood is not supported properly as it enters/exits planer
Solutions:
- Replace worn feed rollers if needed
- Adjust outfeed table height to be level with planer table
- Support long boards at infeed and outfeed to prevent tipping
- Adjust pressure bar parallel to table to evenly hold down stock
- Take very light final passes of 1/64″ or less
Snipe is one of the trickier delta planer problems to fully eliminate, but careful alignment and workpiece support can help minimize it. Taking very light final passes of 1/64″ or less with the grain can also help reduce snipe.
Tearout
Tearout occurs when small splinters of wood get ripped loose during planning, leaving behind a rough, splintery surface. It’s especially common in figured woods like maple or cherry, as well as knotty lumber.
Symptoms:
- Splintery, rough surface with loose fibers torn up
- Small voids or missing spots on the planed board face
Causes:
- Knives are dull or chipped
- Feeding against the grain
- Knots or burls in the wood fiber
Solutions:
- Sharpen, rotate, or replace dull/chipped knives
- Feed with the grain direction to avoid splintering
- Use slower feed speed for problem woods
- Take very light passes under 1/32″
- Apply masking tape over problem areas when planing
Sharpening the planer knives regularly is key to preventing splintery tearout. Slowing down the feed rate can also help, along with taking very light passes of under 1/32″. Applying masking or painter’s tape over knotty areas minimizes tearout as well.
Snails/Terrible Surface Finish
“Snails” refer to the snail-shaped marks sometimes left behind by a planer’s cutting head. The ripples marr an otherwise smooth wood surface, requiring extra sanding or scrap material.
Symptoms:
- Snail-shaped ripple marks across the face of the board
- Wavy, rippled surface instead of a smooth plane
Causes:
- Outfeed table is set too high
- Feed rollers are misaligned
- Debris buildup on cutterhead or chipbreaker
- Damaged or unbalanced cutterhead
Solutions:
- Align outfeed table exactly with planer bed
- Check/adjust roller pressure and parallelism
- Thoroughly clean cutterhead and chipbreaker
- Check cutterhead for dents/damage and replace if needed
- Have cutterhead dynamically balanced if needed
Correctly setting the outfeed table height is key to preventing snails. The rollers should also pull the stock through the planer without shifting to either side. Thorough cutterhead cleaning and balancing fixes problems from debris buildup or damage.
Chip Marks
Chip marks refer to the small divots left behind when debris dings the freshly planed wood surface. They create a pockmarked, uneven appearance to the board.
Symptoms:
- Small divots, dents and voids scattered across the planed surface
- Pockmarked, uneven texture instead of smoothness
Causes:
- Debris buildup on planer bed/rollers is expelled onto stock
- Small knots or defects in wood break loose during planing
- Loose, dangling fibers get rolled into surface
Solutions:
- Check for debris underneath table and thoroughly clean
- Inspect lumber for defects before planing
- Use brush/air compressor to constantly clear table
- Take lighter passes under 1/16″
- Feed at slower rate if needed
Keeping the planer bed and rollers debris-free prevents most chip marks. Inspecting and removing any knots or defects in the lumber prior to planing also helps. Taking lighter passes reduces the chance of debris dislodging.
Snipe at End of Board Only
If you notice snipe marring only the trailing end of boards, the likely culprit is an improperly set outfeed table. Too low, and the board will dip as it exits the cutterhead, resulting in gouges or deeper cuts.
Symptoms:
- Gouges or deeper cuts only at the end of planed boards
- No snipe noticeable at beginning of boards
Causes:
- Outfeed table is set too low compared to cutterhead
- Lack of support for trailing end allows dipping
Solutions:
- Raise outfeed table slightly to match cutterhead height
- Adjust supports to eliminate trailing end dipping
- Take lighter passes of 1/64″ or less
- Hand-support trailing end if needed
Carefully raise the outfeed table in very small increments until it matches the cutterhead height. Also check that the exit end of long boards is properly supported to prevent tipping downward. Light passes again help reduce snipe.
Snipe at Beginning of Board Only
If snipe appears only at the start of planed boards, the culprit is often misaligned or worn infeed rollers. This allows the leading end to dip as it first contacts the cutterhead.
Symptoms:
- Snipe/gouging at the beginning of boards only
- No visible snipe issues on trailing board ends
Causes:
- Infeed rollers are misaligned or height is off
- Worn rollers have uneven pressure/contact
- Insufficient support on infeed end
Solutions:
- Carefully realign infeed rollers
- Replace worn rollers for even contact
- Add extended support for infeed end
- Take lighter passes under 1/16″ depth
Take a close look at the infeed rollers and realign if they are off parallel from the cutterhead. Replace worn infeed rollers that have grooves or uneven pressure points. Adding extra support under the infeed end can also help minimize initial tipping.
Blade Chatter/Vibration
Loud chattering noises and visible vibrations during planing generally stem from problems with the cutterhead itself. Either debris buildup or damage can throw off the smooth rotation.
Symptoms:
- Loud rattling or chattering during planing
- Visible vibration of the blades/cutterhead
- Rippled/wavy surface left on board
Causes:
- Debris is stuck between cutterhead and housing
- Damaged or unbalanced cutterhead
- Loose or worn knives/inserts
Solutions:
- Thoroughly clean cutterhead and check for debris
- Inspect/replace any damaged knives or inserts
- Check cutterhead balance and have dynamically balanced
- Tighten any loose mounting bolts/screws
Carefully inspect the cutterhead for any stuck debris between it and the housing. Remove buildup with compressed air or cleaning tools. Check that blades are securely mounted with no damage. Having the cutterhead dynamically balanced smoothes out vibration issues.
Rough/Fuzzy Grain
When planed surfaces come out fuzzy or rough even after light passes, it generally indicates dull cutter knives. The fibers are being torn out rather than sliced cleanly.
Symptoms:
- Fuzzy, wooly grain on the planed surface
- Splintery texture with raised grain
- Wood fibers look chewed up rather than cut
Causes:
- Knives are dull, chipped, or nicked
- Low cutting speed with dull blades
- Feeding against the wood grain
Solutions:
- Sharpen or replace nicked/chipped knives
- Increase cutting speed for cleaner cuts
- Feed along the direction of grain
- Replace knives in sets to balance
- Apply masking tape over problem areas
Keep knives sharp by honing regularly or replacing inserts as needed. Increase the cutting speed when using fresh sharp knives. Tape over areas prone to fuzz and tearout before final light passes.
Grooved/Rippled Cuts
Grooves running along the length of planed boards indicate issues with worn or misaligned feed rollers. They fail to hold the stock level as it passes the cutterhead.
Symptoms:
- Long grooves or channels in the planed surface
- Rippled texture with highs and lows
Causes:
- Feed rollers are misaligned or uneven
- Rollers have flat spots from wear
- Debris buildup on rollers over time
Solutions:
- Carefully realign feed rollers
- Replace worn rollers for even contact
- Clean rollers and check for debris buildup
- Slow feed rate if needed
Carefully realigning both infeed and outfeed rollers generally solves ripple issues. Replace worn rollers or clean debris from roller surfaces. Slowing down the feed rate can help in a pinch.
Noisy Operation
Loud, grinding noises while running often signal a problem with the cutterhead bearings. Worn bearings can create noise and also leave marks on the planed surface.
Symptoms:
- Loud grinding or rumbling during planing
- Rasping, scrapes noises from cutterhead
- Marks/ impressions rolling across boards
Causes:
- Worn cutterhead bearings
- Debris buildup in bearings over time
- Loose pulley, belt, or component
Solutions:
- Replace worn cutterhead bearings
- Disassemble and clean bearings if needed
- Tighten any loose bolts/components
- Check/replace worn V-belts
Noisy planing typically means worn cutterhead bearings need replacement. Bearings can also be disassembled and cleaned to remove any debris buildup. Check for any loose accessory components like pulleys that need tightening as well.
Rough Outfeed Table
A rough, uneven outfeed table surface can leave scratches or marks on freshly planed boards. Debris, damage, or general wear over time can roughen the outfeed surface.
Symptoms:
- Scratches/marks appear on planed boards
- Debris stuck to bottom side of boards
- Outfeed table feels rough/uneven
Causes:
- Debris buildup on outfeed table
- Table surface worn uneven over time
- Dents, nicks, or damage to table
Solutions:
- Fully clean table to remove debris
- Sand/flatten table if worn uneven
- Use filler to fix dents if needed
- Replace table if excessively damaged
A thorough cleaning is the first step to refinishing an outfeed table surface. For excessive wear, sand or flatten the table to regain a smooth plane. Fill any small dents with epoxy or filler material. Badly damaged tables likely need complete replacement.
Planer Slows or Stalls
When a delta planer suddenly slows dramatically or the motor stalls out, insufficient power is generally the cause. Dirty filters, weak motors, and electrical issues can all cause power loss.
Symptoms:
- Planer motor suddenly slows under load
- Motor stalls out completely during planning
- Power loss when starting on thicker stock
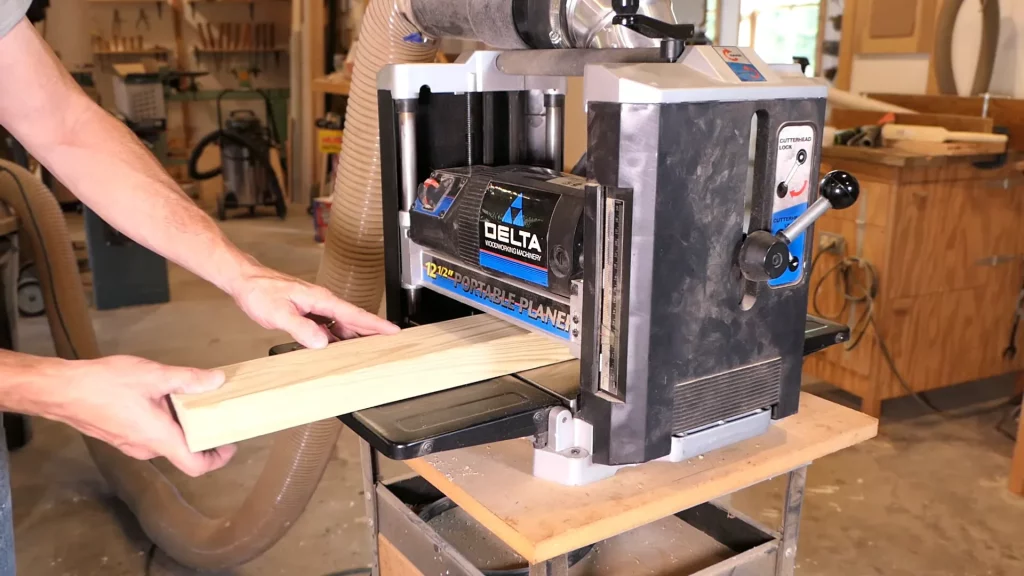
Causes:
- Clogged dust collection filters/bags
- Underpowered motor for requirements
- Electrical issue with circuits/wiring
Solutions:
- Clean or check dust filters/exhaust
- Upgrade to higher HP motor if needed
- Have electrician check wiring for issues
- Reduce amount of material removal
- Take thinner passes under 1/8″
Start by checking dust collection system filters for any clogs and clean thoroughly. For chronic stalling, you may need a motor upgrade to gain more power. Have an electrician troubleshoot circuits for any wiring issues. Taking thinner passes and removing less material per cut can help reduce strain.
Uneven Planing Depth
When planing leaves some areas of a board thinner than others, the cutterhead knives need attention. Worn knives produce an uneven cutting surface and depth.
Symptoms:
- Board surfaces uneven with some areas thinner
- Wavy appearance instead of flat plane
- Areas of heavier/lighter cut depth
Causes:
- Knives are worn unevenly or nicked
- Debris buildup between some knives
- Loose knife inserts/screws
Solutions:
- Sharpen knives evenly or replace worn sets
- Clean debris from knife assemblies
- Tighten any loose components
- Have head dynamically balanced
Closely inspect each knife/insert for uneven wear or damage. Replace worn sets for consistent depth. Remove any debris lodged between knives. Check for loose components and retighten. In severe cases, have an expert dynamically balance the cutterhead.
Delta Planer Troubleshooting Images
Final Words
While no power tool runs perfectly forever, recognizing common delta planer problems helps identify when maintenance or repairs are needed. Pay attention for snipe, tearout, chatter, rough surfaces and other issues impacting results. Keeping knives sharp, components cleaned and adjusted, and properly supporting stock will eliminate many headaches. But when problems do arise, consult this guide to diagnose the likely cause and solution. With proper care and troubleshooting, your reliable delta planer can continue producing smooth, straight boards for years to come.